There are many considerations when selecting an inventory management solution to support omnichannel fulfillment. This is a core feature of most Order Management Systems (OMS) in the market today. Over the last five years we’ve seen specific inventory services also enter the market as composable microservices. All these solutions will provide many compelling business benefits for upgrading your inventory capabilities. A google search on real-time inventory benefits will keep you busy for days evaluating all the cascading impacts having an accurate, real-time view of your available-to-promise (ATP) across your sales channels.
These inventory solutions will tout features such as segmentation, dynamic safety stocks and thresholds. And all these features are required to address the needs of omnichannel retailing. Ironically, it’s not features that retailers seem to be complaining about when thinking about upgrading their inventory capabilities.
At Nextuple, we hear from retailers that it's actually the inventory management basics that are causing them the most headaches.
And so, if any of these ring true for you – read on.
Everyone wants a great audit capability in their inventory service. The problem is that any audit service is a data hog and purge requirements are very different than a simple supply and demand service. You also don’t want that purge activity impacting your core inventory services like ATP and supply and demand updates. In addition, audit activities when launched, can and should be run offline from your main inventory activity. This is why the team at Nextuple created a specific microservice within our Inventory service called Snapshot, Audit, Visibility, and Reconciliation or SAVR.
And let me tell you – it’s a real life SAVR!
Our event driven architecture allows us to decouple the audit activities from the main inventory services. This means your audit team can go crazy interrogating the inventory data during a main shopping demand window on your website.
Coupled with this are specific features we created in the SAVR service to go further than a traditional audit service. Let's dive in.
First off is our snapshot feature. This provides the ability to view the inventory picture for a given snapshot date and time from the past. This visibility helps analyze whether an item was available for selling, and what were the factors impacting it. The snapshot can be used for supply, demand, and availability pictures.
Not only can you understand supply differences across systems, but our audit feature will also allow you to look at the composition of the supply # for the time frame selected. For example, if the supply # is 58 at node 45, the audit feature will not just capture 58 – it will show the transactions in play that created that #.
Another powerful audit feature is the composition of your ATP at a given point in time.
Let's say at 5:00 PM yesterday your ATP went to zero and you stopped taking orders. Most audit systems will allow you to see that in fact yes, your ATP was at zero at 5:00 PM. Our SAVR service will show you the exact transactions or system actions that caused the order stoppage. At any given time, you can go back in time and look at the composition of an ATP. If the ATP is 20, you’ll understand that was because supply was 50 (with corresponding node breakup) and there was demand for 28 (from which sales channels) and you had a safety stock of 2. Most inventory audits do not go this far. In this example, the typical question is, “why was my ATP 20?” which results in a ticket to the IT team who then chases down logs to find the answer.
Many times, when doing root cause analysis on inventory pictures we find out that the system is behaving correctly but that a user or system event has updated the configuration.
But who, when and why?
A modern inventory management platform will have many different configuration settings. An example could be a threshold value, an inventory lock on a node that was created by a no pick, a manual override locking inventory due to a quality issue. Not only does SAVR snapshot track all of these as part of the audit feature, but it has also built in alerts that can be triggered based on these events and many more.
A typical alert use case might be when an inventory lock is created at more than 10 nodes in a certain time frame due to a no pick. This is likely the sign of a store execution issue or improper setting of safety stock on an item.
Taking Snapshots to the Next Level - Reconciliation
The bigger issues typically come across inventory pictures from your OMS and your downstream systems like WMS or ERP or upstream with the Ecomm site. Our SAVR allows you to compare inventory counts across systems to chase down root cause issues. Let's take the following example from a legacy comparison process.
At 7:00 PM let's say you want to compare your OMS inventory and a downstream service like an ERP. You make a query in both systems to give you a supply # but the query is not executed at the exact same time, and this creates noise in your comparison.
Our Inventory Service avoids this issue by using the snapshot date and time available in the uploaded comparison source CSV file for snapshot comparison. It then finds an audit that matches that time stamp and begins the analysis.
In SAVR you are able to upload the results of these two systems and conduct a large-scale analysis of millions of records and it will efficiently find the gaps for further research. This can be done across supply, demand and availability files.
This comparison feature itself is a major risk avoidance tool. During a recent go live of our inventory microservice the client was running our microservice in parallel to the legacy Sterling inventory system. By using the feature, they could gain confidence whether the two systems were in synch or not. In this example an issue was identified through the comparisons, and then the audit feature was used to identify that there was a bug where old historic demand was not getting cancelled by the new system when a line qty was split across more than 1 node. An edge case that would have taken weeks to find with this powerful tool.
Finally, the SAVR service also comes with a natural language chat bot that allows you to query the service. Now you can simply ask “Give me all the inventory locked items in 96.” “Show me the safety stock for item id 5706.” “Show me the last inventory lock created for item id 9805”.
Imagine – crystal clear inventory data and a system that empowers informed decisions. That's the power of SAVR, Nextuple's microservice designed specifically for the complexities of omnichannel retail. SAVR goes beyond basic audits, offering functionalities like historical snapshots, in-depth analysis of supply and availability, and configuration change tracking. It even keeps you informed with alerts and simplifies data reconciliation across your OMS, ERP, and eCommerce platforms. Plus, a natural language chatbot makes it easy to get the information you need. With SAVR, you can finally tame inventory chaos and gain real-time visibility to optimize your omnichannel operations.
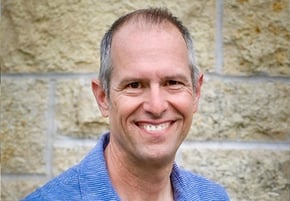